Hot water boilers have operated as the heat centres of our buildings for years. Boiler control/optimisation is high on the list of uptake energy efficient technologies.
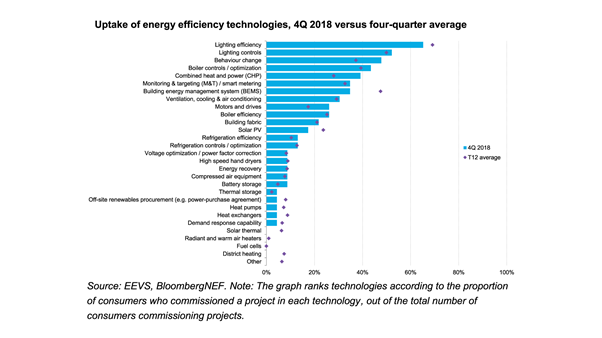
THE PROBLEM:
Quoted instantaneous and advertised combustion efficiencies (sometimes >100%) do not take account of individual Boiler heat loss characteristics during Boiler rest cycles and Boilers can nuisance cycle albeit with high combustion efficiency. Boilers can predictably cycle under low load conditions.
Boilers which lack proper control will nuisance cycle on their own losses. Boiler nuisance cycling is a pervasive problem which often goes widely over-looked by design engineers and building stakeholders.
Boiler cascades and/or condensing/modulating boilers are only a part solution as low water content Boilers without thermal jackets can rapid cycle on low load leading to failure of combustion components and increased maintenance costs.
The problem can be compounded if off-line (lag) Boilers are not hydraulically isolated causing parasitic loads to appear on the lead Boiler through dilution losses in the primary circuit. Pre and post purge losses which accompany excessive Boiler cycling compound these losses.
‘Excessive boiler cycling can lead to early failure of boilers and increased energy use in buildings’ Source: Damianos, Day Ratcliffe 2007.
Boiler nuisance cycling can be easily detected but unfortunately it goes widely over looked by the industry at large. Boiler sequencing through the BMS does not eliminate the problem. Significant savings can be achieved with proper boiler load monitoring/advanced boiler load control.
The elimination of the problem will insure optimum efficiencies, Co2 savings and the extension of Boiler plant lifecycles with reduced maintenance costs.
THE SOLUTION:
M2G represents a breakthrough in boiler load control for LTHW and MTHW systems. European Patent Number 1607820.
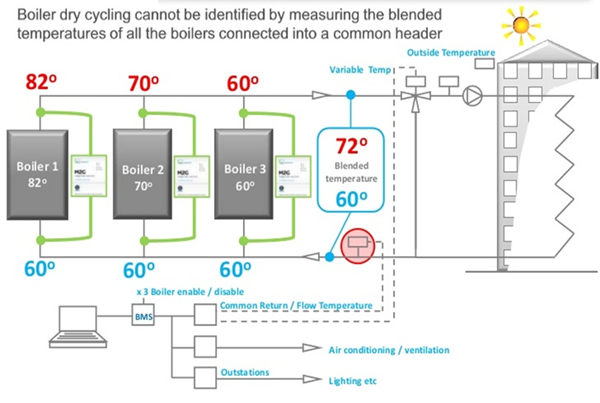
M2G has two digital temperature sensing probes which are attached externally to the each Boiler flow and return pipe-work manifold. The M2G logic provides constant and dynamic monitoring (Movie) of each Boiler every second and references the boiler ‘call for heat’ and ‘boiler off/BMS satisfied’ temperature set points (either variable or set, Boiler or BMS controlled).
M2G places two independent default dead bands on the boiler of F8°C and R3°C. These are adjustable if required through the Engineers Menu on designated boiler control terminal software through the external M2G RS232 interface.
The M2G algorithm will eliminate any response to ‘boiler-only’ heat loss which is not load-demand related. The M2G dead bands are built on existing system set points are refreshed automatically for each and every boiler cycle to identify any nuance in the Boiler or BMS set point strategy.
Importantly, the normal cycle rate of the boiler is matched by M2G during heavy load conditions. In contrast, M2G eliminates any attempt for the boilers to cycle as a result of 1. Standing losses (i.e. convection & radiation losses from the boiler at rest) or 2. Short circuiting (i.e. temperature dilution from the lag boiler when it has not been hydraulically isolated) and 3. Short Cycling (i.e. any boiler response to very low load leading to very short boiler run cycles).
Expected Savings:
Savings greater than 10% can be expected in addition to BMS (optimum start-stop, sequencing and weather compensation). Savings range from 6% – 25% depending on controls and system set up. M2G integrates seamlessly into the boiler/BMS control circuitry on the interlock normally provided by boiler manufacturers. M2G has no maintenance requirements and a 5-year product warranty applies.